The Grundfos CR pump was the world's first multistage in-line pump. This innovative pump is available in a full range of sizes and limitless combinations. Below is a more detailed look at the core components of the CR series pump.
Motor
Grundfos provides many motor solutions depending upon the application and demand. In addition, Grundfos makes its own motors to ensure maximum performance. The ML motors are remarkably quiet and highly efficient. They are also available in the self-regulating MLE configuration, featuring an integrated variable frequency drive.
Cartridge seal
The specially designed cartridge seal increases reliability, ensures safe handling and enables easy service and access.
Shaft seal solutions
The cartridge shaft seal configuration comes in a wide choice of materials. It is available in flushed seal and double seal configurations and can handle temperatures from -40°F to +356°F (-40°C to +180°C).
Connection options
The Grundfos CR can be connected to any piping system.
Dry-running sensor
The patented Grundfos LiqTec™ system eliminates the risk of breakdowns due to dry running. If there is no liquid in the pump, the LiqTec will immediately stop it.
High-performance hydraulics
Pump efficiency is maximized by state-of-the-art hydraulic design and carefully crafted production technology.
Durable bearings
The CR bearings are remarkably long-lived thanks to hardwearing materials and a wide range of options for difficult liquids.
Material options
The CR is available in four different materials: AISI 304/cast iron, stainless steel AISI 304, stainless steel AISI 316, and titanium.
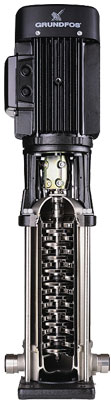 |
The CR is well known for its reliability, its design has all the durability that customers expect from a high-quality multistage pump. The CR series have unique features to ensure unsurpassed reliability: dry-running protection, a unique cartridge seal, and a fulltitanium variant. The virtually endless range of standard and customized CR pumps means that you can find the right CR to provide reliable operation for most any requirement.
Superior dry-running protection
Dry running is the most common cause of pump failure. In most pumps, the shaft seal and bearings will burn out almost immediately if liquid stops flowing in the pump. The Grundfos CR is different as it is constructed using new and alternative materials to bring you the most reliable solution possible. This means that we can equip CR pumps with a shaft seal and bearing system that can withstand extreme heat and friction for longer periods of time. This makes them more forgiving in the event the pump does run dry. If you have situations where you wish to completely avoid dry running the pump Grundfos LiqTec can be installed with your pump which will monitor for liquid 24 hours a day. Available with all CR pumps, the LiqTec is plug-and-play technology which constantly checks that there is liquid in the pump, if it detects the pump is dry it stops the pump immediately.
CR Range and Pump Selection Criteria
CR is available in 11 hydraulic sizes, four basic materials and about one million configurations. You can get CR pumps with magnetic drives, with air-cooled shaft seal chambers, with double shaft seals, etc. Special CR pumps are available for high-pressure performance, for aggressive liquids, and much more. And there is a CR pump for almost any liquid you could possibly want to pump.
The CR range is available in four different basic materials:
CR
AISI 304 Stainless steel with cast iron top and base |
CRI
AISI 304 stainless steel
throughout |
CRN
AISI 316 stainless steel
throughout |
CRT
Titanium
throughout |
Aggressive or
corrosive liquids |
Seawater, hypochlorites, hydrochloric acid, ferric chloride, nitric acid, chromic acid, phosphoric acid |
Abrasive liquids |
Metasilicate-containing cleaning agents, abrasive alkaline cleaners, phosphates |
Toxic or explosive
liquids |
Trichlorethylene, toluene, petroleum, ethyl alcohol, methyl alcohol |
High-viscosity liquids |
Glycols, carboxylates (for cooling), lubricating liquids oils, rapeseed oil |
Hardening liquids |
Water-based paint, glue, vegetable oils |
Crystallizing liquids |
Glycol additives, naphthalene, sugar products (e.g. dextran), salts |
High pressures |
Water treatment, cleaning/washing |
Extreme
temperatures |
Petrochemicals, oils, boiler feed, secondary coolants |
|