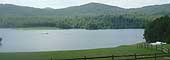 |
Applications |
Automotive |
Biodiesel |
Dairy Industry |
Industrial Wastewater |
Food Processing Industry |
Iron Removal |
Latex Removal |
Metals Treatment |
Mining Industry |
Municipal Wastewater |
Odor Control |
Petrochemical Industry |
Poultry Industry |
Products |
Activated Carbon |
Bag Filtration |
Biological Treatment |
Chemicals (Specialty) |
Clarifiers |
Controls |
Dissolved Air Flotation |
Dewatering |
Evaporators |
Membrane Filtration |
Microbial Bacteria |
Oil/Water Separators |
Ozone |
Pressure Filtration |
Screens |
Separators/Strainers |
Hydrocyclone Separator |
Self Cleaning Suction Filter |
Preliminary Strainers |
Automatic Jet-Disc Filter |
Automatic Jet-Disc Skid Mounted |
Cone Filters |
Tanks |
|
In-Line Separators for Industrial Applications
Use our centrifugal-action separator to remove grit, sand, metal chips, fines, and other solids from liquids. Perfect for use as a pre-filter to extend the life of fine filtration systems. These units require little or no maintenance, as there are no moving parts to fail or wear out, or filter media to clean or replace. The unit only requires a simple purging, eliminating downtime due to cleaning or backwashing. For flows from 6 gpm and retention ratings to 50 micron. |
Features
- Low constant pressure drops
- Piped housings
- Carbon steel or stainless steel
(304 or 316) construction for housings
- All housings are electropolished to resist adhesion of dirt and scale
- ASME code stamp available
- Pipe sizes 3/8 through 6-inch (larger sizes also available)
Options
- Different size and style outlet connections
- Available in Carbon Steel, 304 SS or 316 SS
|
 |

|
How it works:
Fluid enters the pressure vessel tangentially at high velocity. A centrifugal action is created, which forces the solids to separate and enter the sump, while the clean liquid exits up through the standpipe. The solids collect in the sump, and can easily be purged. The operation is so simple, it can be set to automatically purge on a timed interval. |
Typical Applications
- Cooling towers
- Process water
- Food processing
- Chemical processing
- Well water
- Pulp & paper mills
- Mining operations
- Steel mills
- Petrochemical industry
- Power plants
- Protection of spray nozzles and other small orifices
- Chip removal from cutting coolants
|
- Car and vehicle wash systems
- Paint spray booths
- Heat exchangers
- Spray nozzle protection
- Industrial laundries
- Solids recovery
- Parts washing systems
- Pump protection
- Domestic Water
- Recirculating cooling water
- Sprinkler systems
- Quench water
- Pre-filter for seawater
|
 |
Aluminum |
2.7 |
Ashes (Coal) |
2.0 |
Brass |
9.0 |
Bronze / Copper |
8.9 |
Carbon / Concrete |
1.8 - 2.5 |
Coal (Anthracite) |
1.3 - 1.9 |
Earth (Silt / Soil) |
1.2 - 2.0 |
Glass (Crystal) |
3.0 |
Granite / Gravel |
2.5 - 3.0 |
Graphite |
2.3 |
Iron |
7.8 |
Lead |
11.3 |
Limestone |
2.8 |
Manganese |
7.4 |
Nickel |
8.9 |
Sand/Silica/Shale |
2.6 / 2.8 |
Steel |
7.8 |
Tin Ore |
6.4 - 7.0 |
|
Sep-6 |
3/8 |
NPT |
1 |
3 |
6 |
1.8 |
.24 gal. |
Sep-11 |
1/2 |
NPT |
1 |
7 |
11 |
3.4 |
.24 gal. |
Sep-25 |
3/4 |
NPT |
1 |
15 |
25 |
2.5 |
.94 gal. |
Sep-35 |
1 |
NPT |
1 |
30 |
40 |
14 |
.94 gal. |
Sep-75 |
1 1/4 |
NPT |
1 |
55 |
75 |
25 |
.9 gal. |
Sep-80 |
1 1/2 |
NPT |
1 |
60 |
80 |
25 |
.9 gal. |
Sep-130 |
2 |
NPT |
1 |
90 |
130 |
41 |
.87 gal. |
Sep-140 |
2 1/2 |
NPT |
1 |
96 |
140 |
41 |
.87 gal. |
Sep-275 |
3 |
NPT or Flanged |
1 |
200 |
275 |
85 |
1.04 gal. |
Sep-553 |
4 |
Flanged |
2 |
425 |
553 |
175 |
7.81 gal. |
Sep-1265 |
6 |
Flanged |
2 |
985 |
1265 |
400 |
16.26 gal. |
|

SEP-6 THROUGH SEP-275
|
SEP-6 |
3.0 |
14.8 |
4.5 |
1.9 |
.6 |
SEP-11 |
3.0 |
14.8 |
4.5 |
1.9 |
.6 |
SEP-25 |
4.5 |
17.2 |
8.6 |
3.5 |
1.1 |
SEP-35 |
4.5 |
23.6 |
8.6 |
3.5 |
1.1 |
SEP-75 |
4.5 |
23.5 |
8.6 |
4.5 |
1.4 |
SEP-80 |
4.5 |
23.5 |
8.6 |
4.5 |
1.3 |
SEP-130 (2") |
4.8 |
22.6 |
8.6 |
6.6 |
2.1 |
SEP-140 (2.5") |
6 |
22.6 |
8.6 |
6.6 |
1.9 |
SEP-275 |
6.6 |
25.2 |
10.7 |
8.6 |
2.6 |
SEP-553 |
13.0 |
45.2 |
18.0 |
12.7 |
4.1 |
SEP-1265 |
16.4 |
58.0 |
24.0 |
16.0 |
4.7 |
|

SEP-553 and SEP-1265 |
Installation
The separator should be installed in a near vertical position. The unit should be supported by means other than the inlet/outlet piping. First, connect the outlet of the unit to the outlet piping. Then install any supports, such as U-bolts or legs. Next, connect the inlet piping to the inlet. Test for leaks and separation. The unit is now ready for operation.
Purging and Maintenance
Separators must be purged regularly. If they are not, the separated solids will accumulate and overflow the collection area, affecting performance and contaminating effluent.
The operator can manually, automatically or continously purge the collection area of the separator. Manual purging requires that the operator open a simple valve and empty the contents. Automatic purging can be done many different ways, but the easiest is setting a timer to open and close the valve, purging the contaminant on a regular basis. Continous purging simply requires leaving a manual valve partially open at all time, letting the contaminant leak out at a controlled rate. For best results, all purging should be done while the separator is in operation.
|
|
|
|